Linear stages and automation actuators are essential components in additive manufacturing (AM) processes, providing the quick and precise mechanical responses necessary for generating intricate three-dimensional structures. Often referred to as 3D printing, AM has proliferated through the worlds of engineering and industry. It is now one of the leading solutions for next-generation manufacturing challenges like agile tooling, mass customization, and rapid prototyping.
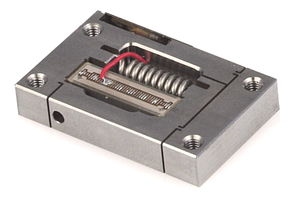
Additive manufacturing and 3D printing are umbrella terms for an increasingly diverse range of mechanical systems. A brief selection of the technologies now available to large-scale manufacturers and hobbyists alike include digital light processing (DLP), fused deposition modelling (FDM), stereolithography (SLA), and much more. Each of these relies on a range of different integrated components to achieve the levels of high throughput and independence that are characteristic of AM technologies. Arguably, none of those components are more important than the automation actuators in the positioning system.
In this blog post, we will explore why precision motion control with linear stages and automation actuators are so important to 3D printer operation.
What is AM (3D Printing)?
Understanding the importance of automation actuators in AM processes first requires a basic understanding of how a typical 3D printer works. The purpose of AM is to convert a three-dimensional CAD (computer-aided design) file into a fully-rendered physical model with little-to-no human intervention. This is carried out by vertically separating the digital model into a series of two-dimensional wafers, which are used to coordinate the position of various mechanical elements (i.e. a printer head).
In essence: AM makes it possible to manufacture functional components and prototypes layer-by-layer directly from a digital dataset. This can help accelerate research and development (R&D), series production, and can enable the development of more complex geometries from challenging materials. These techniques have demonstrated outstanding potential in the plastics industry and are experiencing increasing uptake in more complex fields such as the medical device and pharmaceutical sectors.
As the technology matures, the industry strives to produce printers that can create smaller and smaller details. Here, advancements in linear actuator and motion technology provide the required positioning accuracy and control.
Outlining Linear Stages and Actuators for AM
Linear motion components such as stages and actuators have proven foundational for AM processes, providing controlled linear motion for printing systems in a range of architectures (i.e. heads suspended from gantry systems). Precision linear stages restrict mechanized motion to a single degree of freedom, and the latest designs are capable of resolutions down to the nanoscale. For high speed motion and longest life time, linear motors are ideal. Classical ball-screw designs can also be used, especially for higher forces and when self-locking capabilities are required, lead screws are ideal.
Piezo automation actuators set the gold standard when it comes to precision high-speed dosing. A piezo actuator converts electrical signals directly into a corresponding mechanical response, with sub-nanometer (nm) resolutions and sub-millisecond response times. They are ideal for valve control for micro and nano-dosing, providing both faster response, and higher accuracy compared to solenoid and voice-coil driven systems, with billions of cycles of life time, setting the benchmark for ultra-precise motion control in heavy-use 3D printing.
Automation Actuators from PI
PI is one of the world leaders in the design and integration of precision actuators for demanding areas of application. With a choice of both economical linear positioners and class-leading piezo actuators, we can offer solutions for workshops and facilities of all scales.
If you would like more information about our full product range for AM processes, simply contact a member of the PI team directly.