Why Google Engineers can make better Cameras using PI’s Direct-Drive Hexapod Multi-Axis Motion Platform
Google’s Pixel 2 has one of the most advanced cameras found in smartphones today. In a recent YouTube video by “Nat & Friends” on how Google built the Pixel 2 Camera, PI’s H-860 “shaker” hexapod is shown in a motion simulation application. Modern cameras use electronic image stabilization algorithms to reduce side effects from motion that otherwise would blur images and video. The better a designer can simulate and repeat the actual vibration and unwanted motion generated by typical humans holding a camera, the more effective countermeasures can be devised.
Vibrations and motion typically occur in many degrees of freedom, i.e. there is angular and linear motion in multiple axes often at the same time.
After recording motion profiles using instruments such as accelerometers, and turning them into digital signals that can be replayed on a motion simulator, engineers can then begin to test and fine-tune different electronic stabilization algorithms to come up with the best result for each situation.
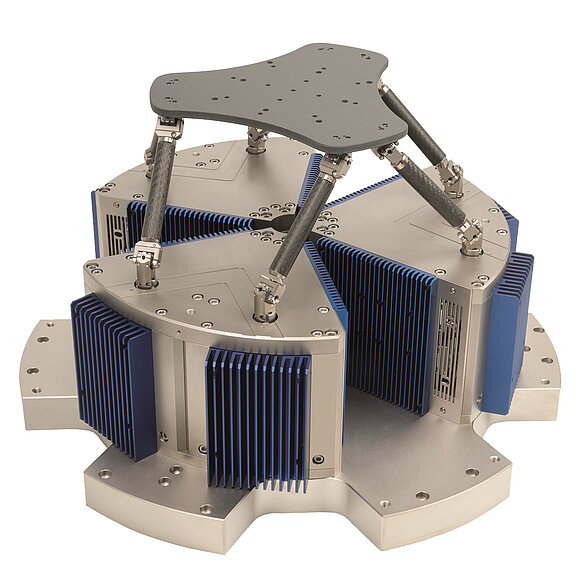
A hexapod platform can provide motion in all six degrees of freedom (X, Y, Z; Pitch, Yaw, Roll), an ideal tool to simulate any type of motion or vibration that occurs in the real world.
Talking about motion and vibration – it is very critical for the hexapod not to add any mechanical vibration of its own to affect the motion profile to be played back.
PI engineers designed a direct drive hexapod with frictionless drives and bearings for just that purpose. Hydraulic, or electric screw drives, always create and transmit additional vibrations onto the motion platform. PI’s approach is based on non-contact voice coil linear motor drives with flexure guides and flexure joints for the 6 “legs”. This design combined with a carbon fiber structure to reduce mass and inertia forms a highly responsive, dynamic, and precise 6-axis motion platform.
Hexapods are parallel kinematic structures and have other advantages over traditional multi-axis motion systems (see bottom of page).
Using the PI’s shaker hexapod platform, Google engineers can simulate unwanted motion and vibration for both still images and video recordings. PI’s hexapod controller and GUI make it easy for software engineers to create any random motion and make the smartphone mounted on its platform move along a predefined trajectory with the frequency content that corresponds to the typical trembling of the human hand. The H-860 voice coil hexapod can provide motion with frequencies to 30 Hz and above and provides linear repeatability of ±0.5 microns in X, Y, Z and angular repeatability of ±9 microradians in the pitch, yaw and roll axes. The hexapod controller and GUI allow predefined motion profiles, such as sinusoidal signals and freely definable trajectories with high path accuracy.
Why Parallel Kinematic Motion Platforms?
Traditional multi-axis stacks are relatively simple in their design, but parallel-kinematics has many advantages. They do however require a more advanced controller to handle the millions of math operations required to take care of the coordinate transformations.
Improved dynamics and stiffness.Traditional multi-axis systems are designed in a way that the top level stage has to be supported by all the stages below it and so on, meaning that the bottom positioner has to carry all the load, significantly reducing its dynamics. All axes carry different loads, with different dynamics making tuning harder since each component has a different natural frequency. With only one common light-weighted platform carried and actuated by six parallel actuators, hexapods provide a very high stiffness and natural frequency. The lower inertia (moved mass) leads to higher dynamics, better responsiveness, and faster settling for all axes.
Freely selectable center of rotation (Pivot Point). In a serial kinematic system, motion is confined by bearings – and the center of rotation is related to the fixed radius of each rotary stage and goniometric cradle used. In order to move the center of rotation, mechanical changes, have to be made or fixturing needs to be modified. With a PI hexapod, a single software command can set the center of rotation to any location inside or outside the hexapod envelope. In PI’s multi-axis hexapod systems, the center of rotation can be changed by a single software command on the fly.
No cable management issues. With traditional multi-axis positioners, as a stage moves, cables need to be dragged along. Friction and torque generated by bending forces contribute to parasitic motions reducing accuracy and repeatability. Parallel kinematic positioners, such as hexapods, avoid moving cables altogether.
No parasitic errors. Stacked axes interact in complicated ways. For example, runout in the x-axis can cause unwanted motion in the y– and z-axes; angular deviation of an axis similarly imparts motion in the travel-directions of the other axes, with magnitude proportional to the distance to the moving axis. And in stacks, that multiplicative lever arm can be large.
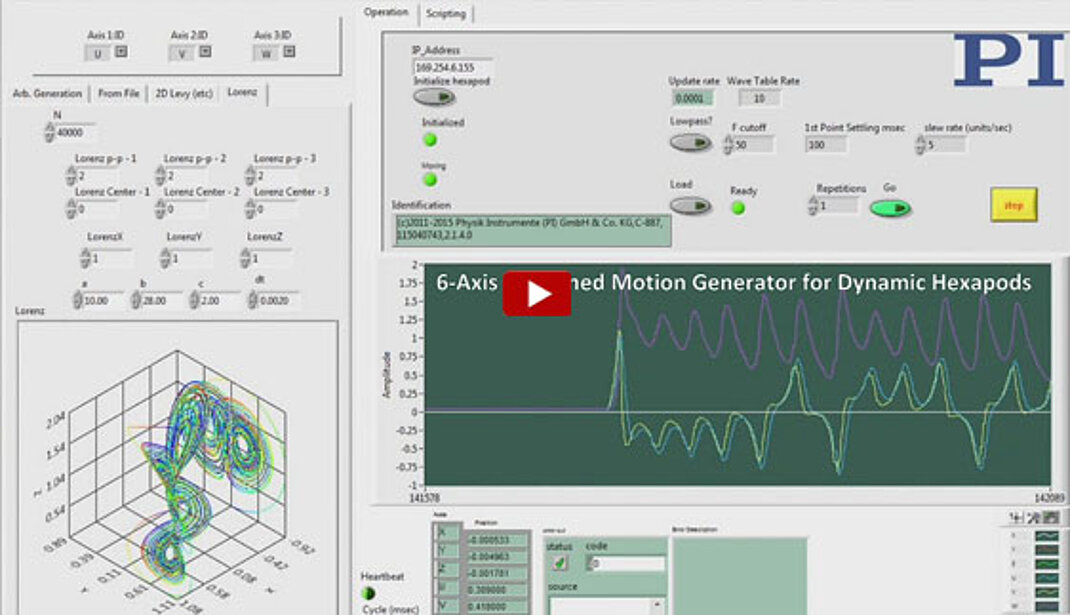