A precision linear actuator is a positioning device that provides motion in 1 degree of freedom. PI designs and manufactures a variety of precision actuators (pushers) including economical stepper-motor driven actuators, high-speed linear motor types for automation and nanometer precise piezo-motor actuators.
While there are many different types of precision actuators, piezoelectric actuators are the first choice when accuracy, speed, responsiveness, and resolution are essential.
PI can help you choose the optimum solution for your special demands from the widest range of technologies :
- Set-and-forget applications benefit from the specific features of piezomotors that provide excellent long-term stability, also for vacuum or nonmagnetic environments.
- Stepper and DC motor solutions are well-established and reliable for both industrial and research use.
- The unique force control option of Voice Coil actuators is essential for touch-sensitive devices.
- Nanopositioning actuators stand for high dynamics and forces as required in shutters or machining processes.
Precision Lead Screw Captive Actuators, Stepper & Servo Motor-Driven
<0.1µm Resolution to 50mm Travel, ~1mm/sec
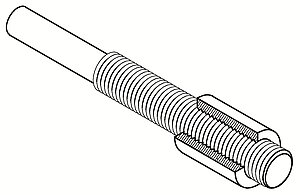
Classical captive motorized actuators with servo and stepper motors are typically combinations of a rotation-type motor and a screw-type actuator.
Lead-screws provide high forces and self locking capabilities, while ball screws are used for higher speed applications with longer service life. Position feedback is available with linear encoders and motor shaft mounted rotary encoders.
Smaller motors are often equipped with gear heads to provide higher torque and resolution, however at the cost of speed.
Actuators with built-in anti-rotation (non rotating tip) are easier to integrate and when used as pushers, do not generate torque or wear at the contact surface.
Low Cost Lead Screw Captive Actuators, Stepper Motor-Driven
To 25mm Travel, 1µm Resolution, to 5mm/sec
Precision Ball Screw Motorized Actuators Servo & Stepper Motor-Driven
To 0.1µm Resolution, Low Friction, To 50mm/sec, Forces to 400N
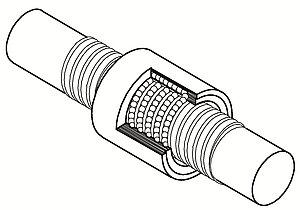
Recirculating ball screws (RBS) provide lower friction and higher velocity than lead screws by replacing sliding friction with rolling friction. Lower friction also means less heat generation when operated at high duty cycles and high velocities. On the other hand, reduced friction also means lower holding forces when powered off.
Motorized actuators with built-in anti-rotation (non rotating tip) are easier to integrate and when used as pushers, do not generate torque or wear at the contact surface.
Fast Voice Coil Actuators with Mechanical Bearings
Velocity to 750mm/sec, to 20mm Travel, to 20N Force
Voice Coil Actuators are based on a single-phase electromagnetic linear motor similar to the driver of a loud-speaker. They provide high velocity with zero wear and motion ranges typically up to 1 inch. The V-273/5/7 family actuators below come with a force sensor option, useful in applications such as switch testing or touch surface sensitivity analysis. The C-413 controller allows on-the-fly switching between force and position mode.
Fast Voice Coil Actuators with Frictionless Air Bearings / Flexures
Zero Wear, Velocity to 1000mm/sec, to 25mm Travel, to 70N Force
These voice coil actuators uses frictionless bearings – either flexures for short travel, or air bearings for extremely straight guiding. Both drive and guiding systems are wear free and clean room compatible.
PI currently offers several types of long travel piezo linear motors and several types of short travel actuators such as flexure actuators, stack actuators, and bender actuators. The drive principle in piezo ceramic motors / actuators is intrinsically nonmagnetic and vacuum-compatible.
Piezo Motor Actuators
Stick-Slip Ratchet Type Piezo Motor Actuators (Screw Drives) are often used for set & forget type adjustments, replacing manual micrometers. They provide high resolution and holding forces, but low speed typically on the order of a few mm/minute.
Stick-Slip Direct-Drive Piezo Motor Actuators (Mini-Rod Drives) are compact ceramic linear motors with forces to 10N and speed to 10 mm/sec.
PiezoWalk® Linear Motors achieve holding forces to 800N and picometer range resolution; however they are more complex and typically used in high-end applications.
For more information on the differences between piezo motors and actuators and their applications, refer to the piezo motion tutorial.
Ultrasonic Piezo Motors are characterized by very high speed of 100's of mm/sec and a very compact design.
Information on vacuum compatible motorized actuators can be found here.
Compact, Low Cost Piezo Ratchet Motor Actuators (Micrometer Replacement)
Set & Forget Applications, to 20nm Steps, to 22N Force
These actuators require some kind external position feedback – the inertia motors provide high resolution, but w/o an internal sensor exact position information is not provided. Unlike conventional stepper motors, the step size in piezo inetia motors is not equidistant.
Captive and Non-captive Versions
The N-422 is a non-captive design with the shaft running through the motor, providing longer travel. The N-412 is a captive design.
The operating principle of a PiezoWalk® linear motor is similar to the principle of biological walking. Motion is generated through a succession of coordinated lift/forward/drop cycles of two or more “legs”. Each cycle can be controlled to provide steps from a few picometers to a few microns of linear motion. With repetition rates of up to 100’s of steps per second, continuous motion up to 15mm/sec can be achieved. These drives are preloaded, self-clamping and achieve exceptional life times.
Ultra-High Resolution Piezo Flexure / Micrometer Actuators & Flexure Actuators
For Fast Step & Settle or Dynamic Scanning Applications, Sub-nm Resolution, up to 1mm Travel
Ultra-High Resolution Piezo Stack Actuators (Short Travel 15 to 180µm)
Forces to 30kN+, Sub-millisec Response, Sub-nm Resolution
Piezo stack actuators provide high forces, high stiffness, and very fast response in the sub-millisecond range, with displacement typically in the 100µm range. Applications: Biotechnology, nano-dispensing, microfluidics, valve control, fast switching and nanopositioning, optics, medical-devices, life-sciences.
These encased piezoelectric actuators are driven by cofired multilayer PICMA® piezo stacks. PICMA® piezo stacks are extremely reliable and survived 100 billion cycles of life-testing and harsh environments in space and on the Mars Rover with no failures.
Preloading a piezo stack inside a case by means of special springs allows the actuator to handle higher tensile forces.
Hermetically sealed actuators with inert gas filling can be used in harsh environments.
Custom actuator designs with larger travel ranges, higher forces or faster response, as well as non-magnetic versions are feasible.
Applications: Piezo actuators can provide high forces and virtually unlimited positional resolution down to the sub-nanometer range. They make for ideal “OEM motion engines” in fields such as biotechnology, nano-dispensing, microfluidics, fast switching and valve control, nanopositioning, optical alignment, microscopy, medical-devices, and life-sciences.
Low Cost Precision Leadscrew / Ball Screw Stages with Stepper & Servo Motors
<0.2 to 0.5µm Resolution, Travel to 300mm, 10mm/sec to 100mm/sec
Classical motorized linear stages, with ball bearings or crossed roller bearings and leadscrew drives.
Lead-screws provide high forces and self locking capabilities while ball screws are used for higher speed applications with longer service life. Position feedback is available with motor shaft mounted rotary encoders.
Direct-drive stepper motors or servo-motor wit gearbox are mostly used to drive the stages.
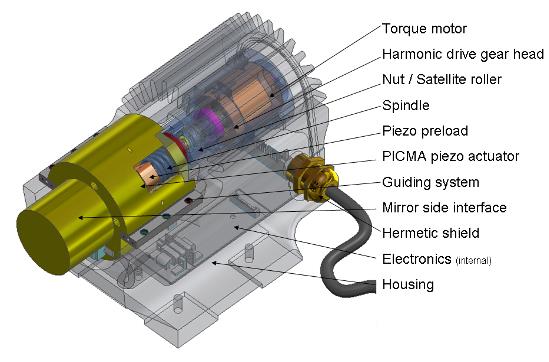
Precision actuators can be customized for force, speed, resolution and travel length to suit varying applications - like adjusting 798 quarter ton segments in the primary mirror of the Extremely Large Telescope (ELT) with nanometer accuracy in the extreme environment of the Chilean Atacama Desert, with a hybrid actuator design. >> More information about ultra-high precision positioning for the ELT.