Piezo-driven active mirrors (tip/tilt motion) and adaptive mirrors (multiple actuators deforming the mirror surface) have been employed in most high-end astronomical telescopes for more than two decades. The resolution gain compared to passive mirrors is typically more than one order of magnitude. Modern telescopes collect light with huge primary mirrors – the larger the mirror, the more photons are collected. For example, the primary mirror of the Subaru Telescope on Mauna Kea, HI, spans 8.3 meters. Even larger telescopes are possible with segmented mirrors, such as found in the E-ELT. Segmented telescopes require nanometer precise motion control to alignment each mirror segment, such as the hybrid drives that are also currently being evaluated.
The light from the primary mirror is then focused onto several smaller mirrors until it finally hits the imaging detector. Earthbound telescopes – in contrast to extra-terrestrial installations such as the Hubble – have to deal with atmospheric turbulence distorting the wave front (an effect that humans perceive as “twinkling”) and wind buffeting that induces vibration in telescope structures. Both effects limit the image resolution. To counteract these limitations, fast, highly precise mechanisms are integrated in secondary and tertiary mirrors controlled by wavefront sensors and fast algorithms analyzing the degree of distortion. The downstream mirrors are used for this because they are smaller and lighter, facilitating the design and improving the performance of the mechanical subsystem – sub-micron linear precision, sub-microradian angular precision and bandwidth in the 100’s of Hz is required to keep up with external disturbances.
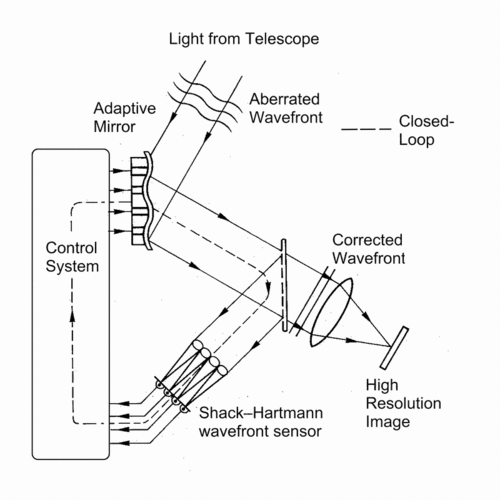
Piezo-ceramics are often used in these active and adaptive systems because they provide high forces, sub-millisecond responsiveness, and atomic scale resolution. The latest project on adaptive optics is currently conducted by a cooperation of the Fraunhofer Institute for Applied Optics and Precision Engineering IOF in Jena, Germany and PI (Physik Instrumente), Karlsruhe, Germany. The goal is to develop a new generation of extremely accurate adaptive optics (XAO), based on 11,000 PICMA® multilayer piezo actuators for the European Extremely Large Telescope (E-ELT) which will be built in the Chilean Atacama Desert in 2024. With a light collection area of almost 1000m², the E-ELT is currently the largest optical terrestrial telescope project.
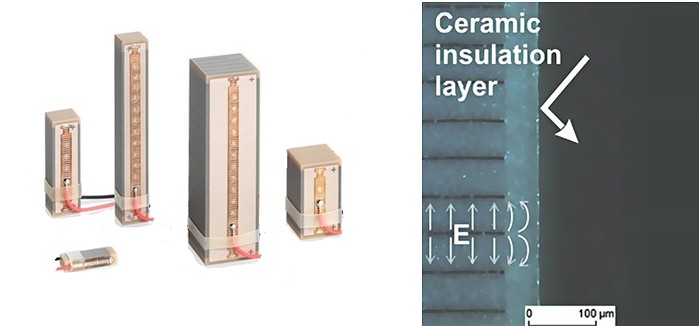
In order to integrate 11,000 actuators, with a <4mm pitch, a new concept is required. PI Ceramic’s PICMA® multilayer piezo actuators have a long track-record for performance. They were tested by NASA/JPL for the Mars Rover and survived 100 billion cycles without failure.
“One of the most important tasks of the telescope is to help us to find out more about exoplanets, i.e., planets that exist beyond our solar system”, explains Stefan Ströbele, system engineer and project manager at the ESO. A highly sensitive camera and a spectrograph are required for imaging and analysis of the atmospheric composition. The XAO mirror system will be an integral part of an adaptive optics system of unprecedented capabilities. The aberrations measured by the wavefront sensor need to be processed and transformed into corresponding position signals for the 11,000 piezo actuators in the deformable mirror and everything needs to happen in real time. The corrected image information allows observation of the finest details on faint celestial objects with a hitherto unattained resolution when compared to terrestrial telescopes currently being used.
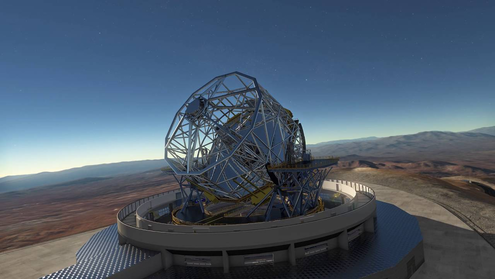
To fulfill the requirements on individual components for this project, which goes well beyond the current state-of-the-art technology, PI combines its longstanding experience in piezo technology with the adaptive optics expertise of the Fraunhofer IOF which will be heading the project. In the planning phase, the emphasis will be on developing the necessary technology for setting up the complex system with up to 11,000 discrete piezo actuators.
Why PICMA® Multilayer Piezo Technology?
PICMA® multilayer piezo technology does away with conformal coatings traditionally used to insulated electrodes in piezo actuators. The conformal coatings used have several disadvantages, such as outgassing. In addition, they collect water molecules like a sponge – leading to increased leakage current and finally dielectric breakdown of the piezo actuators. PICMA® actuators are monolithic, co-fired blocks, consisting of thin tape-cast layers whose electrodes are encapsulated in ceramics, protecting the electrodes against humidity.
Fraunhofer IOF Background Information
The Fraunhofer Institute for Applied Optics and Precision Engineering IOF was founded in 1992 in Jena and develops customized solutions in the field of optical system technology. The expertise of more than 200 employees covers the entire photonic process chain from optical and mechanical design to development of production processes for optical and mechanical components as well as processes for system integration to production of prototypes or small test series. For more information, refer to: www.iof.fraunhofer.com