Advantages and Applications of Custom Direct Drive Motors
Special Voice Coil, 3 Phase Linear & Torque Designs
1. High Dynamics Custom Motors
Instrumentation equipment and precision automation systems manufacturers rely on motion components in applications from optical scanning to micro-mechanical assembly. PI supports these applications with a large variety of standard and custom motion and positioning solutions. A combination of in-house-developed and off-the-shelf mechanical and electronic components, including actuators, guiding systems, position sensors, and motion controllers, allows for great flexibility and performance at reasonable cost.
While gearbox / screw-driven positioning elements provide advantages for vertical and high force applications, direct drive electrodynamic motors are higher speed, zero-wear, and friction-free transmission devices that are preferable in positioning and scanning systems that require high dynamics & repeatability along with reliability over millions of cycles.
In addition to designing piezo-ceramic direct drive linear and rotary motors, engineers at PI have a long history of developing custom motion systems with electrodynamic motors, especially for high-precision and/or high-dynamics applications. The main goal is to achieve specific performance targets that cannot be reached by off-the-shelf products sourced from the market. Here’s a link to a paper dating back to 2000, describing a novel momentum compensated high-speed voice coil linear scanner; other examples include multi-axis Maglev systems, high-speed hexapods, and compact voice coil motors with force and position control.
This blog explains the functional principle and properties of voice coil, 3-phase linear, and torque motors, and provides examples on how performance characteristics of the various motor types can be adapted to the specific requirements of the positioning solution through an individual design, e.g., to achieve a high force density or a compact design.
2. Electro-Magnetic Direct Drives – How do they Work?
Direct drives offer advantages, especially in regard to wear and dynamics, compared to common motor/screw-drive technologies. The reduction of mechanical components, along with the elimination of friction and backlash, result in higher precision and longer service-life. Voice coil, 3-phase linear, and torque motors fall in the class of electrodynamic motors, but differ in their operating principle.
2.1. Voice Coil Motors
Voice coil motors (their name derives from applications in loudspeakers) use the Lorentz force in which the force generated is proportional to the magnetic field strength and to the current of the current-carrying conductors. The generated force acts bi-directionally, depending on the direction of the current.
Cylindrical voice coils are constructed according to the plunger coil principle, i.e., the winding body sits in a field assembly as indicated in Fig. 1. Either the winding body (“moving coil”) or the pot (“moving magnet”) move when energized. Hollow shaft voice coils can be used as a feedthrough and easily integrated in a linear guiding system.
Voice coil motors are mostly used for travel ranges of 1 inch and below when precise scanning motion with high dynamics and relatively high forces is required. For example, the V-522, V-524, and V-528 linear stage series (as shown in Figure 3) are based on voice coil motors from PI.
Simulation tools allow customization and optimization for voice coil motors for different parameters, such as force and motor constant. The motor constant denotes the ratio of force to power loss, or the efficiency of the motor in regard to converting electrical into kinetic energy. The higher the motor constant, the less heat is produced when a certain force is generated. The motor constant is temperature-dependent; with a rise in temperature comes a rise in the winding resistance leading to increased power loss.
PI has developed cylindrical motors, as shown in Figure 4, to maximize the motor constant.
They are characterized by a maximized ratio of motor constant to installation space and can be manufactured in various sizes. Cylindrical motors can be used in fast focusing applications, for moving a measuring head in a metrology system vertically. In combination with a flexure guiding system, especially compact units can be built.
Table 1 shows the performance characteristics of three examples in different sizes.
Figure 5 shows the force displacement dependency. The variation is due to the variable distance between the coils move in relation to the permanent magnets along the travel range. This can be seen in Figure 5.
In order to improve the force / rise time relationship, the voltage can be increased as shown in Figure 6. With higher voltage, the current and force can rise faster leading to better acceleration (jerk) and dynamics.
2.2. 3-Phase Linear Motors
A classical 3-phase linear motor is basically a series of at least three (or a multiple of three) voice coil motors which are controlled, i.e. commutated, according to a position-dependent, fixed pattern. A motor consisting of three coils in a U-shaped magnetic track is illustrated in Figure 7.
Custom encapsulated linear motors for vacuum applications are also available from PI. This results in improved heat dissipation, allowing for higher nominal forces. In addition, the sealing compound ensures that the motor is protected from external damage, e.g., during assembly.
For special applications that require high velocities or fast current rise times, PI can design motors for very high operating voltages up to 600 VDC. In this regard, linear motors benefit from the same effect that was previously described for voice coil motors. Standard industrial high-voltage servo amplifiers are available to drive these motors.
Halbach Arrays
PI can customize the length of the magnetic tracks for OEM positioning systems. Single-sided or U-shaped magnetic tracks are available. U-shaped magnetic tracks achieve higher magnetic field strengths and higher forces than single-sided magnetic tracks. If the magnets are arranged in a Halbach array, the magnetic field strength can be increased by about 10% compared to a North / South Pole arrangement. In addition, the iron counter plate can be omitted in a Halbach array, making these magnetic tracks significantly lighter (Fig 8). The advantages of using a Halbach array also apply to single-sided magnetic tracks. In this case, the use of Halbach arrays avoids the generation of high stray fields on the back of the single-sided magnetic track. PI can provide carbon supports for applications that require ultra-light magnetic tracks.
2.2.1. Iron-Core Linear Motors
Iron-core linear motors are suitable for applications requiring high forces and accelerations with limited installation space. The iron maximizes the magnetic forces and contributes to high thermal stability. To reduce eddy current losses, the iron is laminated and it is mostly made of stacked and insulated transformer plates. The disadvantage of iron-core motors is the attraction force that arises between the iron and the magnets arranged on the opposite side. This is increased further still if a steel linear guide is used. “Cogging” is also a problem since the displacement force varies over the travel range – while this can be minimized by means of special geometries, it cannot be completely eliminated but advanced control algorithms can make it negligible for most applications. An example of an iron-core linear motor is shown in Figure 9.
Ironless and iron-core linear motors are available. For example, motors of both types are used in the V-508 linear stage series. An example of a linear stage of this series is shown in Figure 8.
The sealed motor shown in Figure 10 is an example of a proprietary linear iron-core motor developed by PI.
To ensure a constant force, the linear motors are designed to reach a specified maximum speed. This is shown in Figure 11 with the example of an iron-core linear motor. In addition to other parameters, the maximum speed also depends on the motor voltage provided.
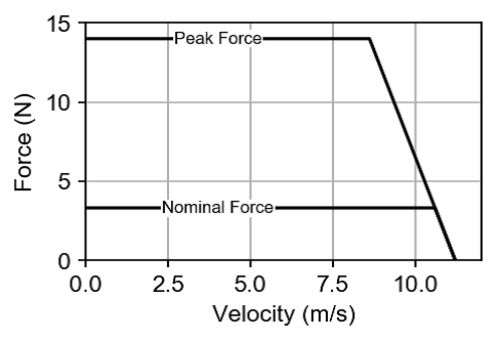
2.2.2. Ironless Linear Motors
Ironless linear motors are suitable for positioning tasks with the highest demands on precision, linearity, and speed stability because they are not affected by cogging. They are also suitable for the smallest installation spaces thanks to their particularly flat design. Power and dynamics requirements can be met by increasing the number or dimension of the motor coils.
In most cases, ironless motors achieve lower nominal and peak forces than iron-core motors. This is due to the lack of thermally conductive metals in the design and the resulting limited heat dissipation from the coils. However, the motors can be protected against overload by means of additional temperature sensors. An example of an ironless linear motor is shown in Figure 12.
The flat motor with a U-shaped magnetic track, shown in Figure 13, is an example of a proprietary ironless linear motor developed by PI.
2.3. Torque Motors
Torque motors are often used in rotation stages for precision positioning and automation applications. Rotation stages based on direct drive torque motors exhibit zero play and backlash unlike worm-gear driven stages. When combined with frictionless air bearings, they provide virtually unlimited service life (Figure 14a). A torque motor is basically a radially designed 3-phase linear motor. In an alternative design, the rotor can also be represented as a rolled-up, single-sided magnetic track, while the stator houses the coils which are embedded in an iron matrix. An example of a custom torque motor developed by PI is shown in Figure 14b.
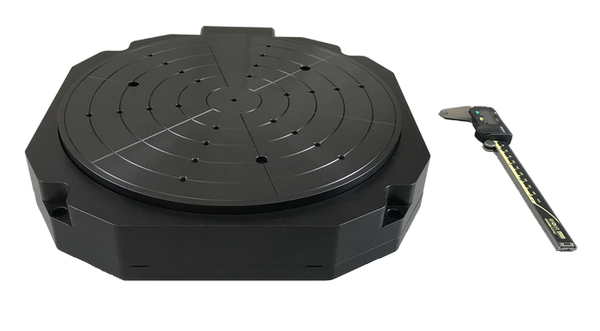
While the magnet length scales linearly, the torque scales quadratically with the diameter. Larger diameters provide more torque and allow for larger apertures that can be used for the passage of laser beams or cables.
In precision positioning, torque motors are mainly used for direct drive rotation stages. Such a rotation stage is shown in Figure 15, stacked on a hexapod. This example shows an extremely flat, highly dynamic, and stable torque motor rotation stage with a very large aperture. The common aperture of the rotation stage and the hexapod can be used, e.g., as a feedthrough.
Fig 15a and 15b show examples of custom 7-axis positioning systems – direct-drive rotary stages mounted on top of 6-axis hexapod stages to add 360 degree rotation capability for alignment and precision automation applications.
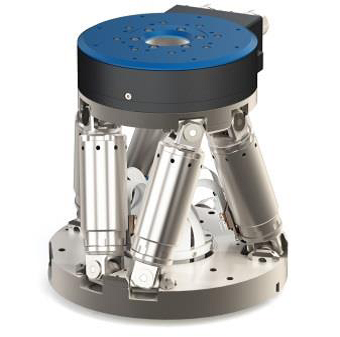
3. Summary
With the in-house expertise to develop proprietary motors and with the core technologies needed for a complete positioning solution, such as sensors, guides, and motion controllers, PI offers its customers competitive solutions with performance characteristics that are optimally adapted to the requirements of the application. Figure 17, for example, shows an application that combines different motor types. The multi-axis setup for autofocus applications shown consists of an X and a Z axis. The X axis, for example, holds a workpiece that is to be machined on a V-508 linear stage. As a supplement to the commonly used piezoceramic drives, the voice coil Z axis enables long travel ranges up to several millimeters. This is important, among other things, for laser material processing. Travel ranges of 1 to 7 mm are typically also required for multiphoton fluorescence microscopy and deep tissue microscopy. Furthermore, voice coils offer particularly high maximum speeds which can, for example, be used to increase throughput when using “scanning-on-the-fly mode” in digital slide scanning processes.
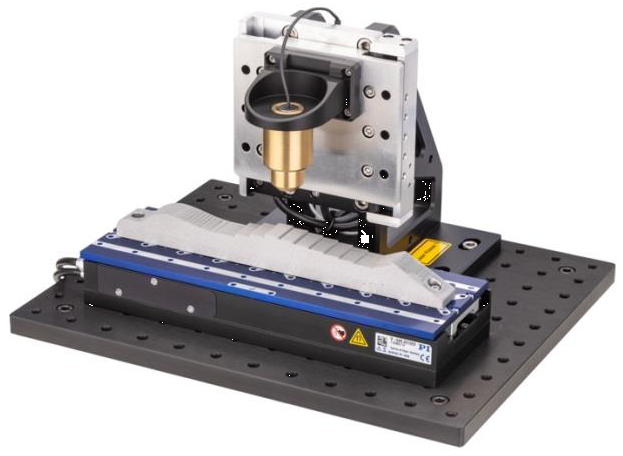
However, thanks to PI's vertical range of manufacturing and technological range, PI is the ideal partner even when customers only require one single component of a positioning solution.
Authors:
Dr. Nico Bolse is Product Manager for PIMag® magnetic drives and motorized precision positioning systems at PI’s headquarters in Karlsruhe, Germany. Stefan Vorndran is VP of Marketing at PI USA.