PILOT - Enabling the Highest Performance Precision Automation Systems in the World
Advanced motion control algorithms perform rapid tracking and ultrafast fast step and settle operations.
The familiar voice of the narrator extolls the virtues of the inherent technological innovation evident in the rapid acceleration and precise braking of a performance car. These critical features serve as important criteria in car selection and are worth careful attention in precision motion systems as well, especially when short, high acceleration moves or external signal tracking motion is required.
PI has developed PI Lead Optimized Translation (PILOT) Technology to push the bounds of performance into new domains for direct drive stages used in applications with short high acceleration moves requiring rapid settling, and tracking applications with moves following an external signal such as in autofocus systems.
In this overview, we present an example of results from short highly dynamic moves of a mass of 2.7 kg with tight error bands using repeated 500nm and 50µm continuous steps. The results shown below are using PILOT as noted for best error characteristics and to achieve dynamics in a compact stage form factor enhancing motor performance while reducing motor heating. An advantage of PILOT is that it gives the same dynamics with less error, less motor current, and less injected heat—preventing a problem instead of compensating for it after. PILOT technology can be applied to both linear motion and rotational motion.
Ten successive steps of 500 nanometers with an artificial 5 millisecond delay applied to each. The blue trace is the profiled motion and the yellow trace is stage position. When viewed at 1µm per division, the two are nearly perfectly overlapped. Note also the time to complete 10 such moves is 200msec and complete time scale here is a single second.
PILOT vs standard: On very tight inspection (200nm/div), the advantage of the PILOT controlled motion (left) is clearly visible in both step & settle timing and error characteristics, compared to the same system operated without the PILOT algorithms (right).
For comparison, the stage was loaded with an additional mass of 6kg. The graph shows 500nm steps (100nm/div) with only slightly reduced rise time performance due to the additional load. The yellow trace (stage position) is still tightly following the profiled motion (blue) – indicating excellent tracking performance.
Same 50µm moves as above but 5X higher zoom (10µm/div) - the error is still negligible with PILOT control
A distinct advantage of cutting edge PILOT controlled motion also applies to motor current. Motor current generates heat, which negatively impacts performance and may restrict the use of compact linear or rotary positioning stages because motors are not sufficiently large enough for applied payload under required dynamics. Here we show how PILOT affects commanded motor current under the same move timing and/or frequency of motion.
Motor current traces related to commanded moves: PILOT control (green) vs standard control (purple). The graph shows ten rapid moves, perfectly overlaid, with identical move times. With PILOT control, the error characteristics are improved and the motor current required is reduced by 25%.
The above tests were run with a V-551 linear motor stage (shown in XYZ configuration below) and an A-814 motion controller. PI provides a large variety of linear stages for applications ranging from industrial precision automation to super-resolution microscopy.
XYZ configuration of V-551 linear motor stage
The V-551 linear motor stage is capable of performing 0.5nm steps as shown above (version with ultra-high resolution PIone linear encoder).
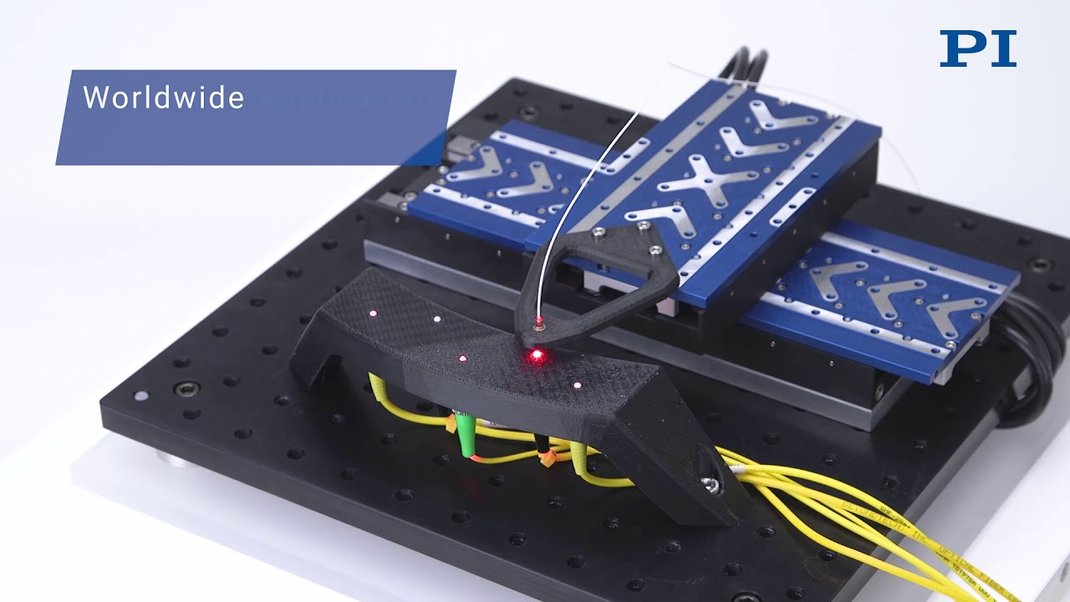