Point-Cloud Surface Reconstruction: What 3D Laser Manufacturing and Lidar Measurements have in Common
How PI supports Additive Manufacturing and Laser Materials Processing Applications
Deep in the jungles of Northern Guatemala, an ancient Mayan city complex is being revealed beneath a forest canopy; ground features are captured and reconstructed in a series of topological points that encode surface information in a 3D point cloud via LIDAR measurements. At the same time, a similar point cloud is forming from a white light interferometer in a sterile white and glass laboratory complex investigating tribological properties of titanium alloys. These two disparate applications, and many others like them (using both contact and non-contact surface measurements), share 3D Point Clouds as a data convention.
What happens though when the goal turns from characterisation toward fabrication of and on such surfaces? Point clouds are merely a collection of discrete data points, typically in a delimited text format of ordered triples. Forming trajectory paths for fabrication processes requires a surface reconstruction that can be made into flexible layers, containing specific intra-layer process paths. These process paths must be adaptable to both subtractive (ablating features into/from a surface) or additive (material extrusion, dispense, etc.) fabrication methods. Adaptability is necessary since specific processes impose parameter bounds that place different demands on process speed, layer infill, layering heights, layer process ordering, etc.
Here, we examine a point cloud with a periodic surface structure. Applying a Screened Poisson Surface Reconstruction, we build a triangulated/faceted mesh out of the point cloud*. The fidelity of the cloud to the surface is at least in part related to measurement resolution and the mesh to the cloud relies on variables such as Reconstruction Depth, Minimum Number of Samples and Interpolation Weight. Here we show a point cloud and corresponding meshed surface. Once properly meshed, the surface can be saved in STL format and imported into SPC Software.
After direct import to SPC, transformations can be applied such as scaling (potentially for miniaturisation or magnification correction), rotational transformation, and location in the coordinate space of the stages. Machine vision is also supported for alignment/overlay.
The imported STL is shown in PI/ACS SPC software with good fidelity to point cloud. SPC features multiple layering and infill options with user-defined inter-layer spacing required for flexible additive/subtractive processes. Layering information can be isolated and previewed in the model as shown (or without model in the view). Here, we select and preview a single process layer in yellow (with applied-infill).
PI/ACS SPC software offers multiple layering and infill options with flexible user-defined inter-layer spacing. Layering information can also be isolated and previewed as well in the model as shown (or without model in the view). Additionally, the surface can be false-colored to more easily identify topological features.
False coloring can be applied to the STL to help identify topological features. Here, a color gradient shows the surface topology variation. Deep red shows the highest points on the STL and deep blue shows the lowest.
The device specific process parameters can be selected (for automatic motion synchronised triggering of a laser or dispenser/extruder) with independent process speed and jump speed for shorter process times. Finally, the 3D window will update the process as it runs, so you have a real-time representation of the model during fabrication.
All of these features are available in PI’s standard and custom gantry multi-axis systems and stages, operated with our motion controllers using ACS (with Ethernet, EtherNet/IP, and EtherCAT connectivity).
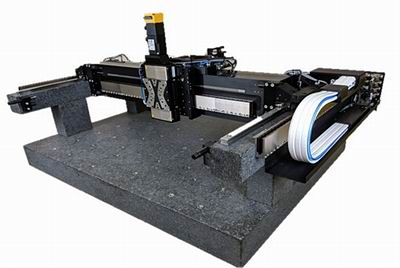
*Citations:
P. Cignoni, M. Callieri, M. Corsini, M. Dellepiane, F. Ganovelli, G. Ranzuglia | MessLab: an Open-Source Mesh Processing Tool | Sixth Eurographics Italian Chapter Conference, page 129-136, 2008
M. Kazhdian, H. Hoppe | Screened poisson surface reconstruction | ACM Transactions on Graphics (TOG), 32(3), 29, 2013