What is a Difference between a Gantry System and a Split-Bridge?
Gantry Systems (Cartesian Robots) and Split Bridges in Automation
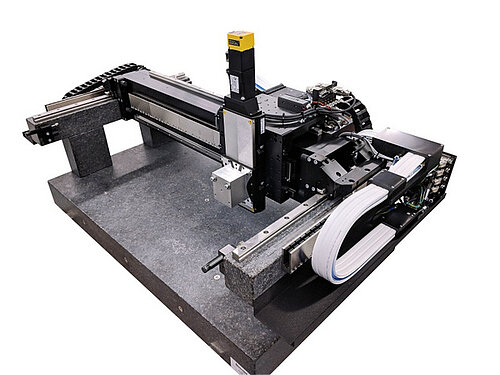
Gantry motion systems and split bridge motion systems are often used in industrial production, testing, and additive manufacturing. A gantry usually consists of a base plate (often granite) and two parallel rails (for the Y-axis, usually linear motor-driven), and a cross axis (bridge axis) riding on the two lower motor-driven linear rails.
A vertical axis can be added on the bridge axis to provide Z-motion. Gantry systems are very useful, when overhead motion is required and a sample cannot be moved – typical for 3D printing processes where the printed sample needs to be stationary for maximum stability and accuracy. Also, when a large sample needs to be mounted to a very flat surface, the gantry has an advantage, especially when a precision ground granite base is used. Another advantage of a gantry system is the possibility to compensate for orthogonality errors. This requires a smart motion controller that can drive the two parallel motors independently, generating a virtual rotation axis (Theta-Z) that can be used for error mapping.
A Split Bridge system can be less complex than a traditional gantry system because synchronization of the two lower linear axes is not required. Either an XY stage is used on the bottom with a Z stage mounted on a fixed bridge, or the X and Y motion stages can be split, with the Y axis on the bottom and the X-axis mounted on the fixed bridge. A vertical axis can also be mounted on the X-axis.
A split bridge can be used when the sample to be tested or manufactured does not have to be stationary or does not require to be mounted on a large, extremely flat base.
Most Gantry Systems are specifically adapted to each application, but based on a modular system to save design time. Customizations include travel ranges, Z-stages, cable management, threaded insert locations, welded bases, and vibration isolation systems. With many years of in-house design and manufacturing experience, PI’s engineering team can scale existing designs to provide a tailored solution to the customer’s project in a short time.
PI’s largest portfolio of precision positioning and motion control technologies, along with 50 years of experience, amount to many advantages for customers in industry and research. In addition to a large variety of drive technologies and guiding techniques (including piezo ceramic motors, voice coils and 3-phase motors, air bearings, flexures and magnetic levitation) - as well as sensor technologies (capacitive, piezoresistive, interferometric) - customers benefit from access to the highest performing motion controllers from our partner, ACS. PI’s service and support offices around the world round make sure you and your application are covered.