Laser material processing continuously advances the state-of-the-art in fields spanning from medical technology (e.g., laser drilling holes in tablets to provide controlled release of drug delivery) to semiconductor manufacturing (e.g., laser annealing for reduced feature sizes). Progress stems from advances in the performance of the laser as well as the motion control and automation system directing the beam and/or moving the parts to be processed quickly and precisely to the exact location at the exact time. Speed and timing are crucial for the laser, the positioning system, and the exact synchronization of multi-axis motion with the firing sequence of the laser.
Readers can probably instantly recall videos on order of magnitudes panning down from celestial bodies to sub-cellular microscopic levels. At the finer end of these scales, where microns and nanometers matter, PI is a world-leader. Each day in technical discussions around the globe, the words micron and nanometer are spoken thousands of times with innovative companies and world-leading research institutions. The focus at PI isn’t just on ultraprecise, it’s also on ultrafast and equally important are terms like picosecond, femtosecond, and attosecond.

Producing components with functional structures and geometries at micron and submicron scales absent of collateral damage is guiding the next generation of laser processes; ultrafast lasers manufacturers and machine builders play a key role here. Ultrafast lasers have wide-ranging application potential in ablative (direct material removal) and non-ablative processes across a spectrum of brittle, flexible, organic, alloy, and composite materials.
In particular, laser ablation has distinct benefits across a spectrum of materials when using picosecond or femtosecond lasers for direct removal. Here, high ablation rates can be achieved with optimum process (optimum fluence, small focal spot sizes, and <10 PS, pulses) with minimal to no Heat Affected Zone (HAZ). The use of short-pulsed lasers results in clean and highly localized laser ablation with a lower risk of mechanical or thermal damage to the workpiece. These short-pulsed lasers are capable of resolving very precise features to the sub-µm scale and single layer removal in the nanometers. Ultrashort pulses are enabling so-called ‘cold ablation’. This reduces the chance of heat build-up that would spread from the processing point where the laser energy is directly absorbed and preventing negative thermal effects (HAZ).
The advantages of femtosecond laser ablation of glass (vs nanosecond) are compelling (image source: www.intechopen.com)
The use of ultrafast lasers can, therefore, be highly effective in ultraprecise micromachining of many materials, such as polymers, which are very susceptible to collateral damage from heat accumulation. There are also many nonablative processes that can take advantage of these lasers. For example: Chemically Strengthened Glass (CSG) cutting, Femtosecond Laser Induced Chemical Etch (FLICE), Fiber Bragg Grating (FBG), Inscription, and Two-Photon Polymerization (TPP).

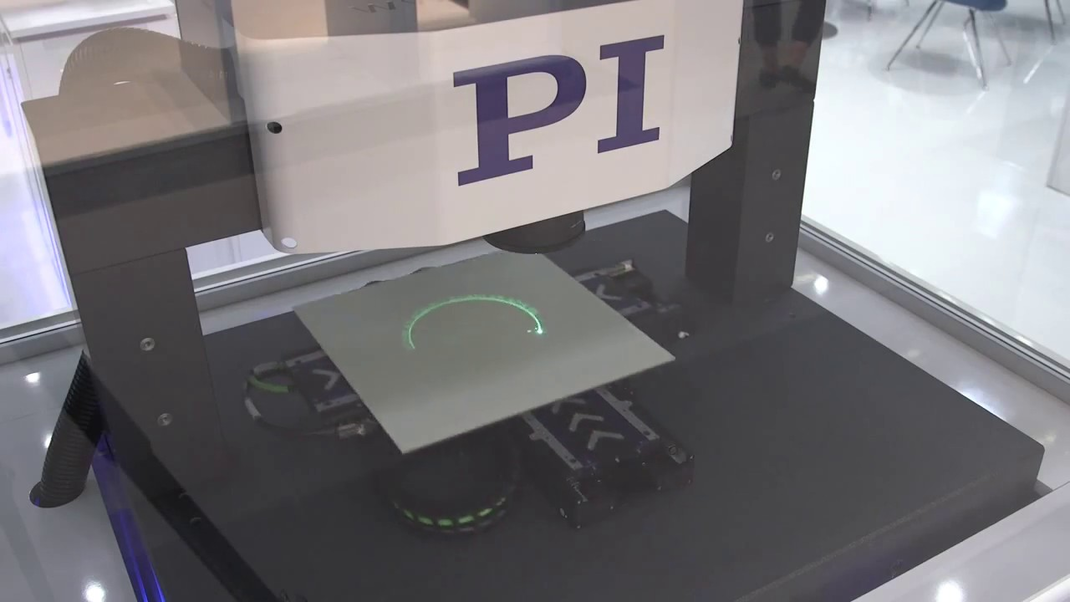

PI has a complete catalog of motion hardware, software, and synchronization solutions for use in ultrafast laser materials processing, including Laser Control Module with advanced features, such as fixed distance firing (used with pulse pickers), advanced trajectory building/following algorithms, customizable system level control software working direct from CAD (STL and DXF format) to process, G-Code and sealed/air-purged multi-axis configured motion systems to overhead gantry platforms.
A rounded rectangle is run at high speed in an ultrafast glass cutting process using V-508 linear motor stages in an XY configuration. The results shown are ServoBoost assisted and the reduced error characteristics are obviously maintaining high speed while minimizing error (enabling higher throughput).